Exploring Table Linen Factory: Craftsmanship Unveiled
Ever wondered how those elegant table linens in hotels come to life? Welcome to our deep dive into the world of a table linen factory. From the initial selection of raw materials to the final touches on the finished product, we’ll take you on a behind-the-scenes tour. Imagine walking through a factory where every thread is chosen with care and every stitch is a testament to craftsmanship. Curious about how it all happens? Let’s unravel the mystery together and discover the secrets behind creating high-quality table linens.
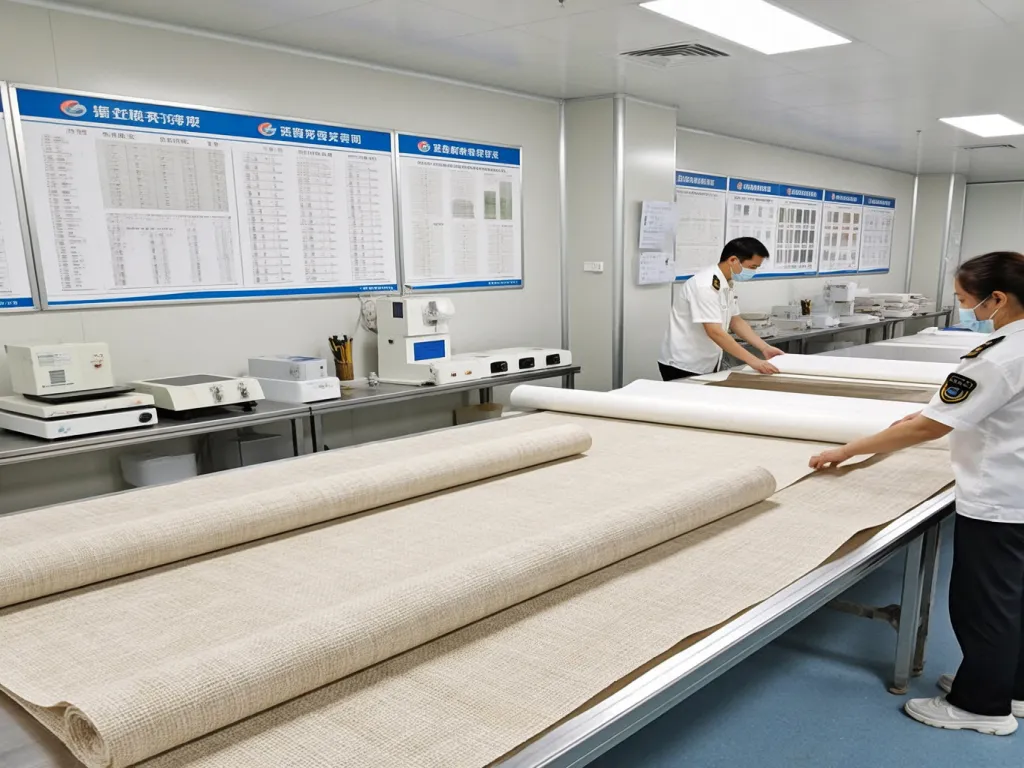
Raw Material Selection and Sourcing: The Foundation of Quality Table Linens
When it comes to crafting top-notch table linens, the journey begins with the selection of raw materials. At our table linen factory, we understand that the quality of the final product hinges greatly on the materials we start with. So, let’s dive into the world of table linen raw materials and see how we ensure only the best make it into our production line.
The primary raw materials we work with include cotton, linen (derived from flax), and polyester. Each of these materials has its own unique set of characteristics that make it suitable for different types of table linens. Cotton, for instance, is known for its softness, breathability, and durability. It’s a popular choice for both casual and formal dining settings. Linen, on the other hand, exudes elegance and sophistication. It’s highly absorbent, making it ideal for hot climates, and it has a natural luster that adds a touch of luxury to any table. Polyester, although a synthetic fiber, offers several advantages such as wrinkle resistance, colorfastness, and ease of care. It’s often blended with cotton or linen to enhance the performance of the fabric.
Now that we’ve covered the main raw materials, you might be wondering how we ensure their quality. Well, it all starts with our rigorous supplier selection process. We understand that the quality of our raw materials is only as good as the suppliers we work with. That’s why we go to great lengths to vet potential suppliers before entering into any partnerships.
Our supplier evaluation criteria are comprehensive and multi-faceted. We look at factors such as the supplier’s reputation in the industry, their production capabilities, quality control measures, and sustainability practices. We also require suppliers to provide detailed information about their sourcing practices, ensuring that the materials they supply are ethically and sustainably sourced. For a deeper understanding of supplier evaluation criteria, you can refer to this insightful blog post which highlights the top five criteria you cannot overlook.
Once we’ve shortlisted potential suppliers, we conduct on-site audits to verify their claims and assess their operations firsthand. During these audits, we inspect their production facilities, review their quality control procedures, and speak with their staff to get a better understanding of their commitment to quality. Only those suppliers who meet our stringent standards make it onto our approved supplier list.
Even after a supplier has been approved, we don’t rest on our laurels. We maintain close relationships with our suppliers and conduct regular follow-up audits to ensure that they continue to meet our quality requirements. We also work closely with them to develop new materials and improve existing ones, staying at the forefront of industry trends and innovations.
In addition to our supplier selection process, we also have strict quality control measures in place for the raw materials we receive. Every batch of materials is inspected upon arrival at our factory. We check for factors such as color consistency, fabric weight, thread count, and any defects or imperfections. Only materials that pass our rigorous inspection process are used in our production line.
By investing time and effort into raw material selection and sourcing, we’re able to ensure that our table linens are made from the highest quality materials available. This not only enhances the performance and durability of our products but also gives our customers peace of mind knowing that they’re investing in a product that’s built to last.
Cotton: The Versatile Staple
Cotton is undoubtedly one of the most popular raw materials for table linens. Its softness and breathability make it a comfortable choice for diners, while its durability ensures that it can withstand regular use and washing. At our factory, we source cotton from reputable suppliers who specialize in growing high-quality cotton varieties. We pay close attention to factors such as the length of the cotton fibers, as longer fibers generally result in stronger and more durable fabrics. We also consider the growing conditions and farming practices used by our suppliers to ensure that the cotton we use is both environmentally friendly and socially responsible.
Linen: The Elegant Choice
Linen is synonymous with luxury and elegance. Its natural texture and luster add a touch of sophistication to any table setting. However, working with linen can be challenging due to its tendency to wrinkle and its relatively high cost. At our factory, we’ve developed techniques to overcome these challenges and maximize the benefits of using linen. We source our linen from suppliers who are experts in processing and finishing linen fabrics, ensuring that the final product meets our high standards for quality and appearance.
Polyester: The Practical Alternative
Polyester offers a practical alternative to natural fibers like cotton and linen. Its wrinkle resistance and colorfastness make it a popular choice for settings where easy care and durability are important. We blend polyester with other fibers to create fabrics that offer the best of both worlds – the comfort and natural feel of cotton or linen combined with the practical benefits of polyester. Our suppliers use advanced blending techniques to ensure that the resulting fabrics are uniform in quality and performance.
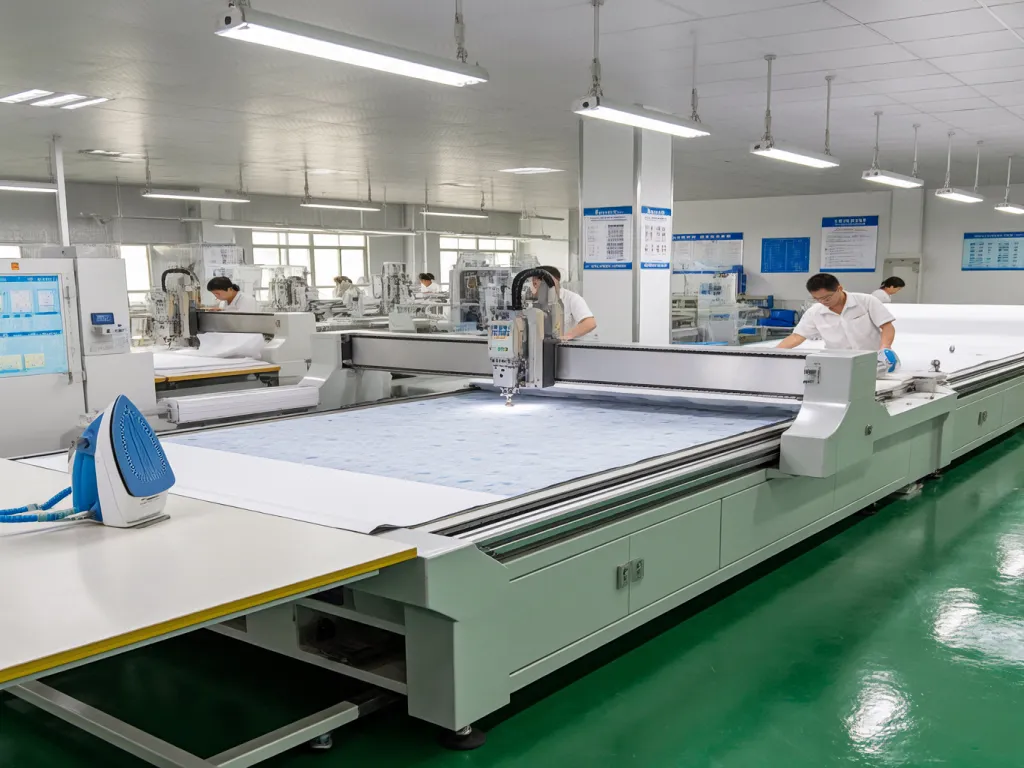
Production Process Details: From Cutting, Sewing to Finishing, Elaborating Every Step of Table Linen Production, Showcasing Advanced Production Equipment and Technology of the Factory
Now that we’ve talked about the importance of raw materials, let’s dive into the heart of our table linen factory: the production process. From the moment the fabric enters our factory doors to the moment it’s packaged and ready for shipment, every step is meticulously planned and executed. Today, I’ll take you on a virtual tour of our factory, explaining each stage of the production process and highlighting the advanced equipment and technology we use to ensure the highest quality products. So, are you ready to see how table linens are made? Let’s get started!
Cutting: Precision is Key
The first step in our table linen production process is cutting. This might seem like a straightforward task, but in reality, it’s a highly technical process that requires precision and accuracy. We use state-of-the-art cutting machines that are programmed to cut the fabric according to the exact specifications of each order. These machines are capable of cutting multiple layers of fabric at once, ensuring consistency and efficiency. Before cutting, our team carefully reviews the order details, including the size, shape, and quantity of table linens required. They then prepare the fabric by laying it out flat on the cutting table, ensuring there are no wrinkles or folds that could affect the cutting accuracy. Once everything is set, the cutting machine gets to work, slicing through the fabric with precision and speed. The result is perfectly cut pieces of fabric, ready for the next stage of production. Have you ever wondered how table linens maintain their consistent size and shape? It all starts with this precise cutting process. For more insights into the precision required in hospitality linens, you can refer to this article.
Sewing: Combining Artistry with Technology
After the fabric has been cut, it’s time for sewing. This is where our skilled artisans come into play, combining their craftsmanship with advanced sewing technology to create beautiful and durable table linens. We use high-speed industrial sewing machines that are capable of stitching at incredible speeds while maintaining the highest quality standards. Our sewing team is trained to handle a variety of stitching techniques, from basic straight stitches to more complex decorative stitches. They pay close attention to detail, ensuring that every seam is neat, even, and strong. In addition to traditional sewing methods, we also utilize modern technology such as computerized embroidery machines to add intricate designs and patterns to our table linens. These machines allow us to create custom designs with precision and speed, giving our products a unique and elegant touch. Whether it’s a simple hem or a detailed border, our sewing team ensures that every table linen is crafted to perfection.
Finishing: Adding the Final Touches
Once the sewing is complete, the table linens move on to the finishing stage. This is where we add the final touches that enhance the appearance and functionality of our products. Our finishing process includes several steps, such as ironing, pressing, and quality inspection. First, the table linens are ironed to remove any wrinkles or creases that may have formed during the sewing process. This gives them a smooth and polished look. Next, they are pressed to ensure that all seams and edges are flat and even. This step is crucial for maintaining the shape and structure of the table linens. Finally, each table linen undergoes a thorough quality inspection. Our quality control team checks for any defects, such as loose threads, uneven stitching, or fabric flaws. Any products that do not meet our strict quality standards are rejected and sent back for rework. This ensures that only the highest quality table linens leave our factory. Have you ever noticed how some table linens seem to have a perfect finish? That’s the result of our meticulous finishing process.
Advanced Equipment and Technology
Throughout the production process, we rely on advanced equipment and technology to ensure efficiency, precision, and quality. Our cutting machines, sewing machines, and finishing equipment are all top-of-the-line, designed to handle the demands of high-volume production while maintaining the highest standards. In addition to our machinery, we also utilize advanced software and systems to manage our production process. From order tracking to inventory management, our technology helps us streamline operations and ensure timely delivery of our products. We are constantly investing in new technology and equipment to stay ahead of the curve and provide our customers with the best possible products and services. Our commitment to innovation and technology is what sets us apart from other table linen factories. For a broader view of the table linen market and technological advancements, you might find this market analysis insightful.
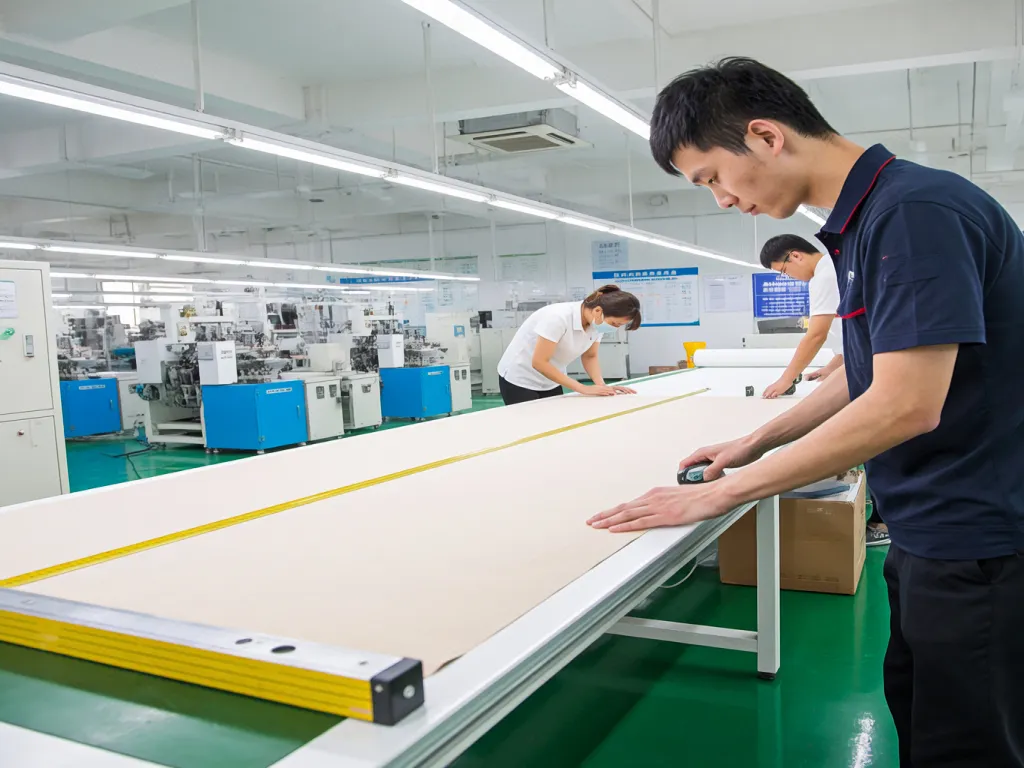
Quality Control and Inspection: Ensuring Every Table Linen Meets High Standards
When it comes to hotel table linens, quality is everything. Our table linen factory understands this all too well and has implemented rigorous quality control measures at every stage of production. From the moment raw materials enter our factory to the final inspection before shipment, we leave no stone unturned in ensuring that every table linen we produce meets the highest standards. Let’s take a closer look at how we achieve this.
In-Process Quality Checks
During the production process, we conduct multiple quality checks to catch any issues early on. Our skilled workers are trained to inspect each table linen as it moves through the various stages of production. For instance, during the cutting process, we ensure that the fabric is cut accurately according to the specifications. Any fabric that doesn’t meet the exact measurements is immediately set aside for reevaluation. Similarly, during sewing, we pay close attention to the stitching quality. Loose threads, uneven seams, or any other signs of poor workmanship are not tolerated. Our sewing machines are regularly maintained and calibrated to ensure consistent and high-quality stitching.
In addition to visual inspections, we also use advanced testing equipment to check for factors like colorfastness, shrinkage, and fabric strength. These tests help us identify any potential problems that might not be visible to the naked eye. By catching these issues early, we can make the necessary adjustments and avoid costly rework later on.
Final Inspection Before Shipment
Once a table linen has completed all the production stages, it undergoes a final, comprehensive inspection before it is packaged and shipped. This inspection is carried out by a dedicated team of quality control experts who have years of experience in the industry. They examine each table linen with a fine-tooth comb, looking for any defects, imperfections, or deviations from our strict quality standards.
During this final inspection, we check for things like the overall appearance of the table linen, the quality of the hemming, the accuracy of the pattern placement (if applicable), and the overall fit and finish. We also perform additional tests, such as checking the fabric’s resistance to stains and wrinkles. Only those table linens that pass this rigorous final inspection are deemed ready for shipment.
Continuous Improvement and Feedback Loop
Our commitment to quality doesn’t stop at the final inspection. We believe in continuous improvement and have a robust feedback loop in place. After each batch of table linens is shipped, we gather feedback from our customers. This feedback helps us understand if there are any areas where we can improve our products or processes.
We also conduct regular internal audits of our quality control procedures. These audits help us identify any gaps or inefficiencies in our system and take corrective actions promptly. By constantly striving to improve, we ensure that our table linens not only meet but exceed the expectations of our customers.
So, the next time you’re looking for high-quality hotel table linens, you can rest assured that our table linen factory has gone the extra mile to ensure that every piece you receive is of the highest quality. We take pride in our work and are committed to providing you with products that you can be proud to use in your hotel.
Advanced Testing Equipment
To ensure the quality of our table linens, we invest in advanced testing equipment. For example, we use colorfastness testing machines to check how well the fabric retains its color after washing. This is crucial for hotel table linens, as they need to withstand frequent washing without fading. We also use shrinkage testing equipment to measure how much the fabric shrinks after washing. This helps us adjust the initial cutting dimensions to account for shrinkage, ensuring that the final product fits perfectly. By using these advanced testing tools, we can guarantee that our table linens meet the highest quality standards. For a deeper understanding of quality control in textiles, you can refer to this sample report on quality control.
Skilled Workforce and Training
Our skilled workforce is another key factor in our quality control process. We hire workers with experience in textile manufacturing and provide them with ongoing training. This training covers not only the technical aspects of the job but also the importance of quality control. Our workers understand that their attention to detail can make a big difference in the final product. They take pride in their work and are committed to producing table linens that meet our high standards. Regular training sessions also keep them updated on the latest industry trends and best practices.
Supplier Collaboration for Quality
We also collaborate closely with our suppliers to ensure the quality of our raw materials. Our quality control team works with suppliers to establish strict quality standards for the materials they provide. We conduct regular audits of our suppliers’ facilities to ensure that they are meeting these standards. By working together with our suppliers, we can maintain a consistent level of quality throughout the entire supply chain. This collaboration helps us avoid any quality issues that might arise from using substandard raw materials. According to a market report from Grand View Research, effective supplier collaboration is a key factor in maintaining high-quality standards in the table linen market.
So, there you have it—a glimpse into the fascinating world of a table linen factory. From the meticulous selection of raw materials to the stringent quality control measures, every step is crucial in delivering top-notch products. If you’re in the market for premium hotel textiles, our factory stands ready to meet your needs with unwavering dedication to quality. Ready to elevate your hotel’s dining experience? Explore our range of table linens and let us help you make a lasting impression. And who knows, your next visit to a hotel might just feature linens crafted by us!